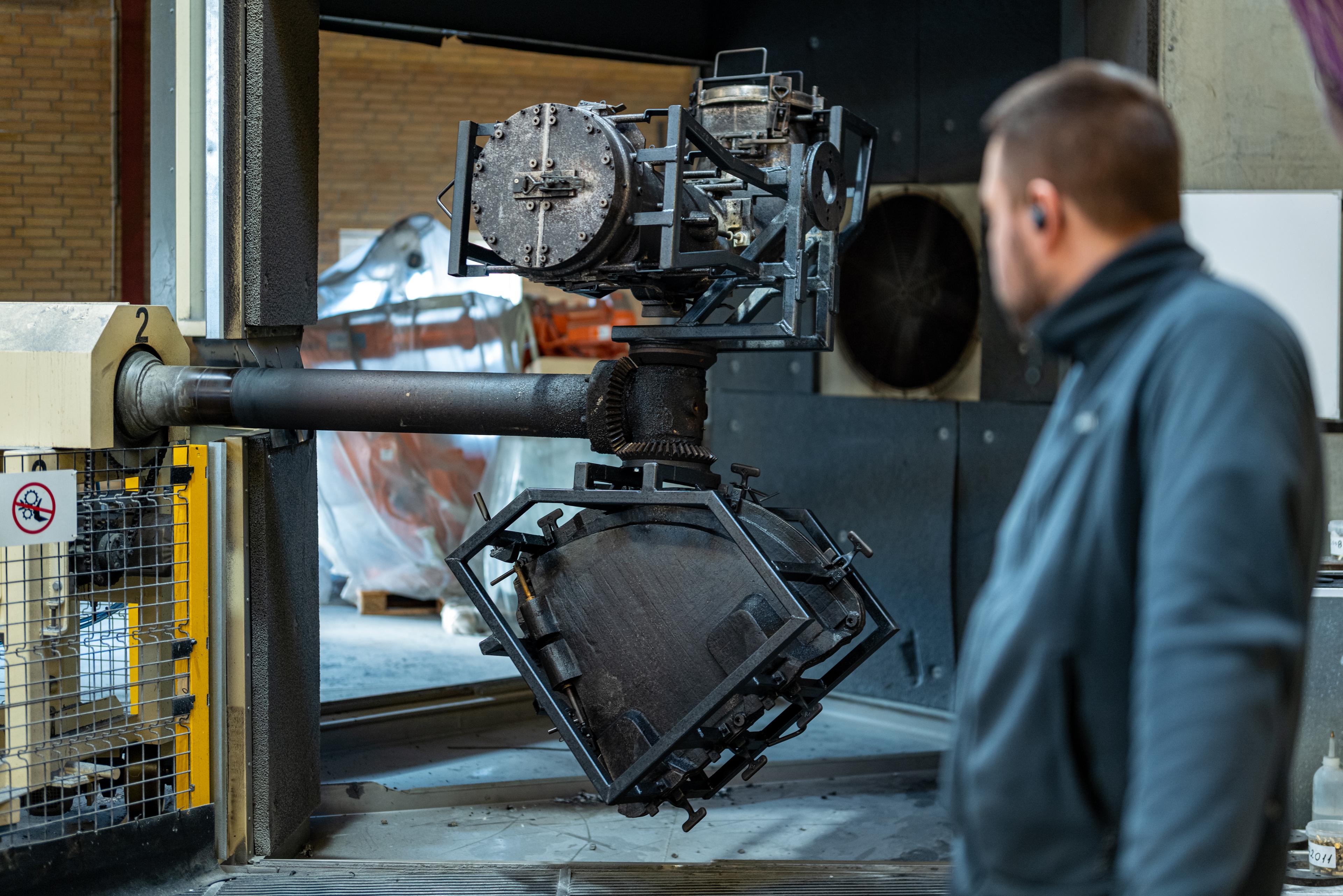
Rotational Moulding
Seamless hollow parts for small- to medium-series production
What this solution offers
Our rotomoulding machines rotate biaxially while gently heating powder inside the mould, creating stress-free, one-piece parts with uniform walls. This method excels at buoyancy products, tanks, complex ducts and fenders – areas where Gibo Plast and Dan-Hill-Plast hold market-leading know-how . We process polyethylene, flame-retardant PP, and conductive grades; multi-layer tooling enables foam-core or barrier layers for chemical resistance. Inserts, threaded bosses and graphics are moulded in during the cycle, eliminating extra labour. Typical series span 30 to 3,000 units, perfectly bridging the gap between prototyping and injection moulding.
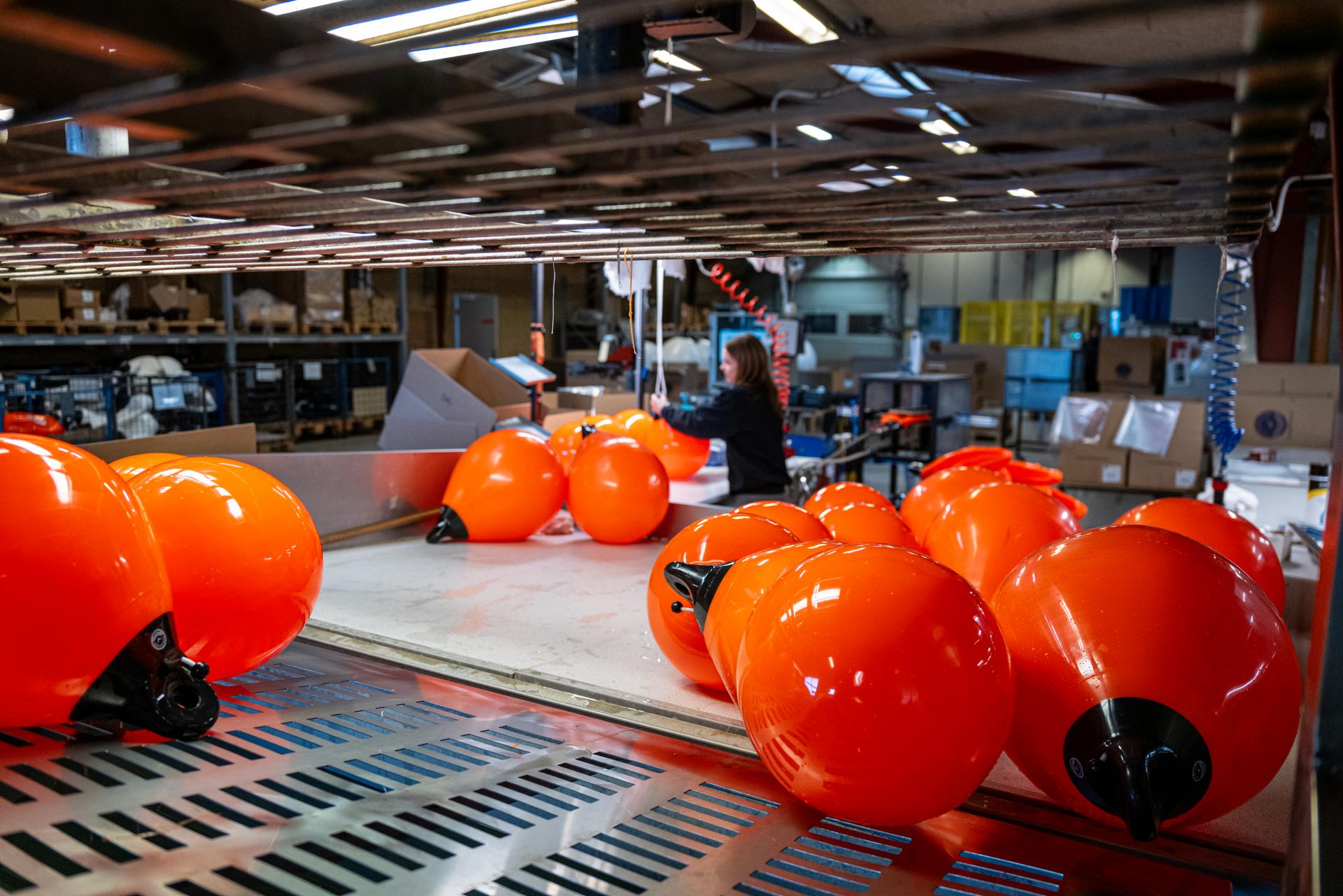
Key Benefits
- Truly seamless: No weld lines means zero leakage points.
- Low tooling cost: Sheet-metal or cast-aluminium moulds.
- Large size capability: Parts up to 4 × 2 m manufactured locally.
- Material versatility: UV-stable, foamed or recycled resin options.
- Integral features: Metal inserts and graphics fuse in-cycle.