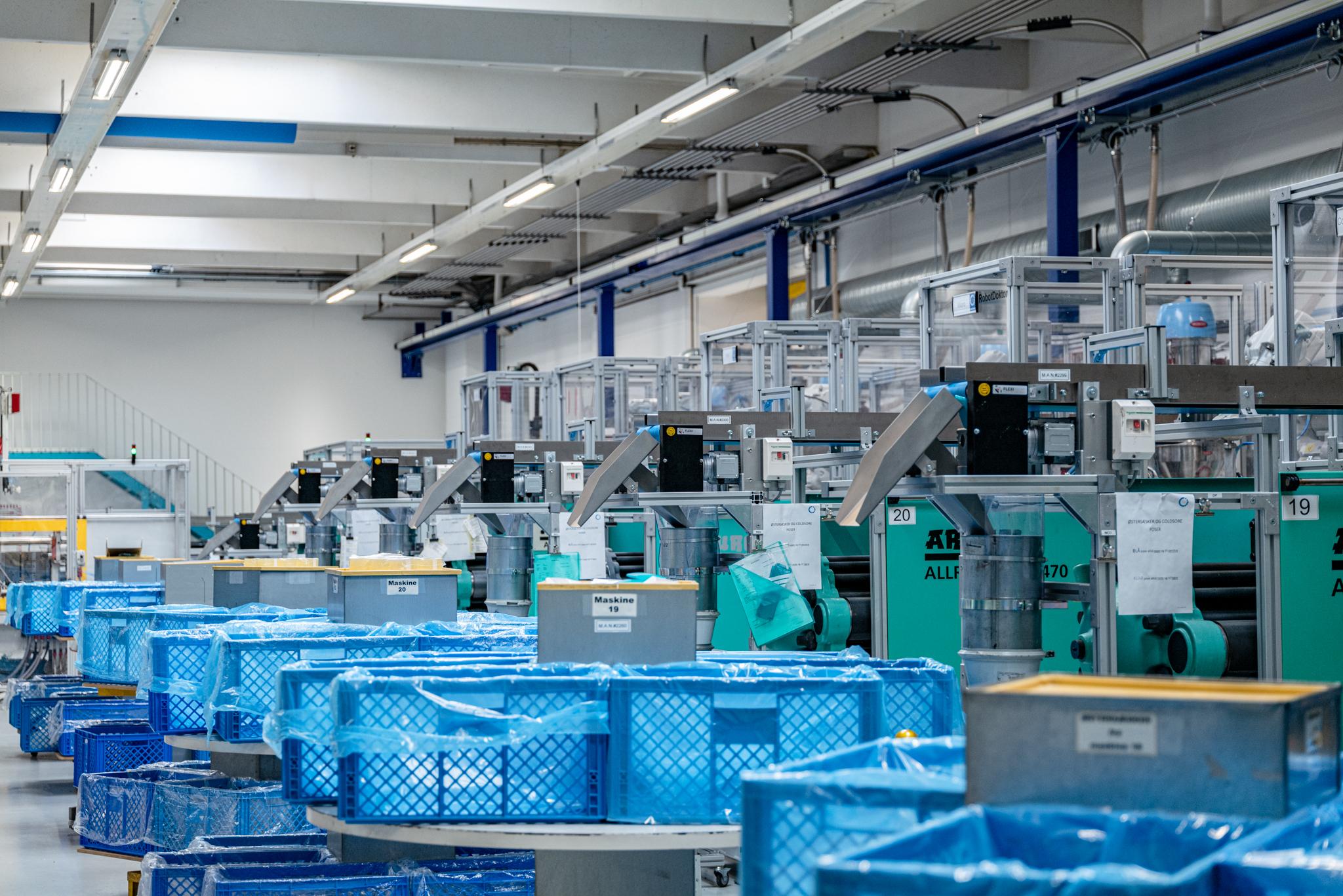
Injection Moulding
Precision components from 480+ machines worldwide
What this solution offers
With more than 480 injection moulding machines, including 50 two- and three-component presses, SP Group is among Northern Europe’s largest independent moulders. Servo-electric presses up to 1,500 t make technical parts for Healthcare, Cleantech and Foodtech.
Cleanroom Class 7 & 8 cells produce medical disposables under ISO 13485, while vertical rotary tables handle insert-moulded electronics. Automation cells integrate vision inspection, laser engraving and packaging, pushing OEE above 85 % and meeting FDA/GAMP validation.
We source, test and qualify steel moulds globally, giving customers the optimal balance between lead-time and lifetime shots.
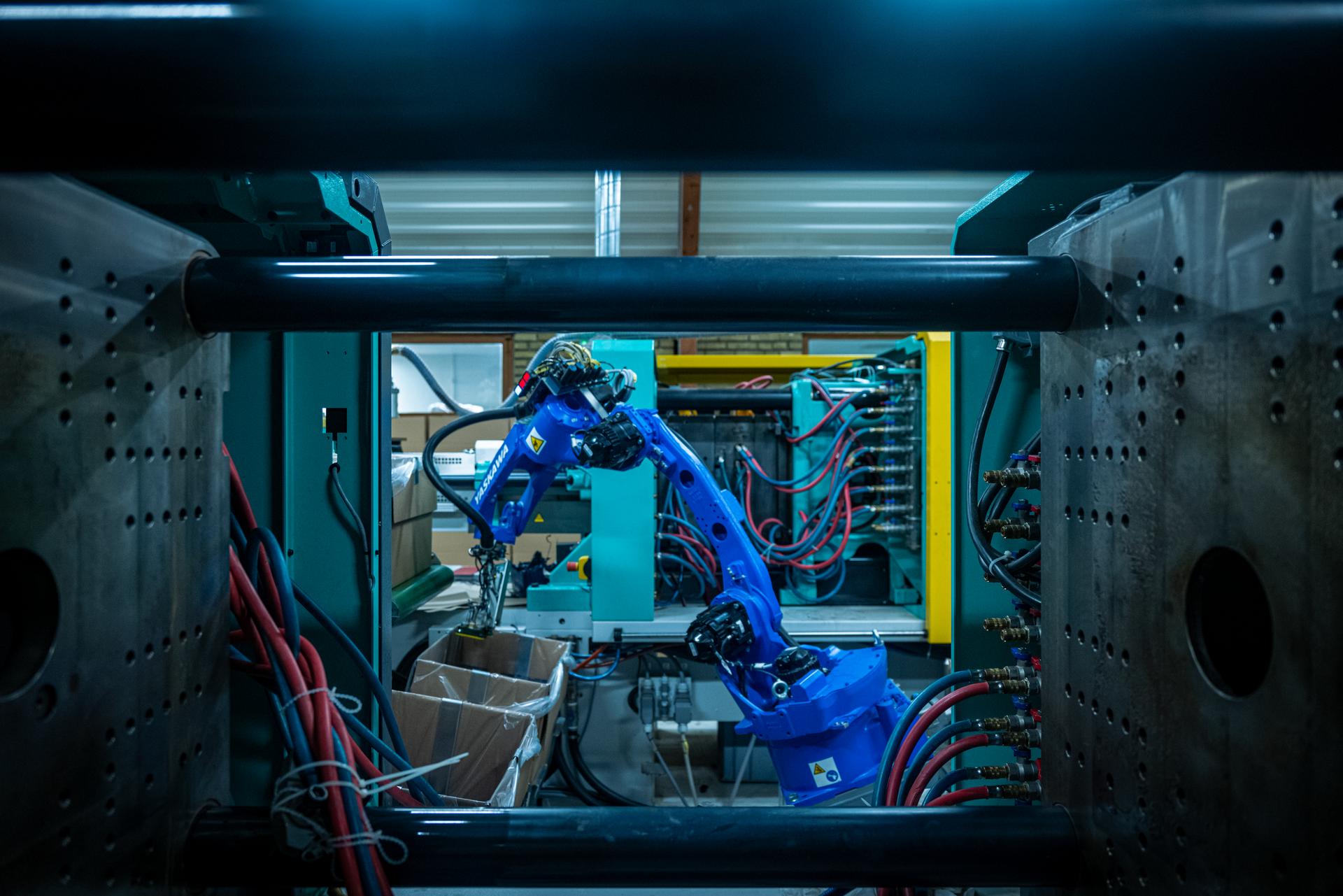
Key Benefits
- Micron-level accuracy: Vital for medical and fluid-handling parts.
- Multi-material options: Hard/soft over-moulding, liquid silicone, metal inserts.
- Scalable economics: From pilot to millions with the same team.
- Regulated-industry compliance: ISO 13485, MDR and FDA support.
- Global footprint: Identical processes in Europe, Asia and USA.